Rail Mounted Gantry (RMG) cranes are pivotal in various industrial settings, particularly in ports, container yards, and intermodal terminals. These cranes are designed to lift and move heavy loads over a wide area, making them essential for efficient operations in facilities where large volumes of cargo are handled. However, the efficiency of an RMG crane is not solely determined by its existence but is greatly influenced by its specifications. Understanding how these rail mounted gantry crane specifications impact working efficiency can help businesses optimize their operations and achieve better outcomes.
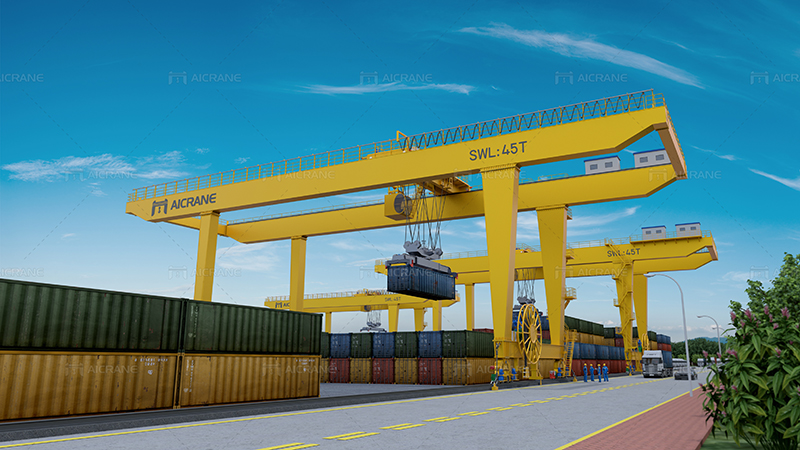
Lifting Capacity
One of the most critical specifications of a rail mounted gantry crane is its lifting capacity. This refers to the maximum weight the gantry crane can safely lift and move. The lifting capacity is crucial because it directly affects the type and volume of loads that the crane can handle.
Impact on Efficiency: If the lifting capacity of the RMG crane matches the demands of the operation, it can handle the workload efficiently without overloading. On the other hand, a gantry crane with insufficient lifting capacity will require more trips to move the same volume of cargo, leading to increased operational time and reduced efficiency. Conversely, an overly powerful gantry crane might be underutilized, leading to inefficiencies in terms of energy use and operational costs.
Optimization Tip: To ensure optimal efficiency, businesses should carefully assess their operational needs and choose a gantry crane with a lifting capacity that aligns with the heaviest loads they expect to handle regularly.
Span Length
The span length of an RMG crane is the distance between the rails on which it operates. This specification determines the width of the area that the gantry crane can cover.
Impact on Efficiency: A gantry crane with an appropriately sized span length can cover the entire working area without requiring repositioning or multiple cranes to cover different sections. This reduces the time and labor needed to move loads across the facility. However, if the span is too wide for the intended application, it could lead to unnecessary costs and space usage, while a span that is too narrow may limit the crane’s reach, forcing operators to relocate the crane more frequently.
Optimization Tip: The span length should be chosen based on the width of the working area and the layout of the facility. Ensuring that the gantry crane’s span covers the entire area without excess can help streamline operations and improve overall efficiency.
Lifting Height
The lifting height of an RMG crane is another crucial specification that dictates how high the gantry crane can lift its load. This is particularly important in environments where containers or materials are stacked vertically.
Impact on Efficiency: Adequate lifting height is essential for maximizing the use of vertical space in a facility. In container yards, for instance, the ability to stack containers higher can significantly increase storage capacity and improve the flow of goods. If the lifting height is insufficient, it could limit the vertical stacking capability, resulting in inefficient use of space and potentially increasing the time needed to access or store items.
Optimization Tip: The lifting height should be determined based on the maximum stack height required in the facility. Matching the gantry crane’s lifting height to the vertical storage needs will help in utilizing the available space efficiently and reducing the time spent on handling operations.
Speed Specifications
Speed specifications, including hoisting speed, trolley speed, and crane travel speed, are fundamental factors that influence the overall efficiency of an RMG crane.
Hoisting Speed: This refers to how quickly the heavy duty gantry crane can lift and lower a load. Faster hoisting speeds enable quicker loading and unloading, which is vital in high-volume operations.
Trolley Speed: The trolley speed dictates how fast the crane can move the load horizontally along the gantry. Higher trolley speeds reduce the time taken to position loads, contributing to quicker turnaround times.
Crane Travel Speed: This speed determines how fast the entire crane can move along the rails. In large facilities, a higher crane travel speed is crucial for moving between different sections quickly.
Impact on Efficiency: Faster speeds generally lead to higher throughput and reduced operational time. However, it’s essential to balance speed with safety and precision. Excessive speed without adequate control can lead to mishaps and damage to goods or equipment.
Optimization Tip: Speed settings should be adjustable to match the specific requirements of the task at hand. For instance, high-speed operations may be suitable for low-risk, repetitive tasks, while slower, more controlled movements might be necessary for handling delicate or high-value items.
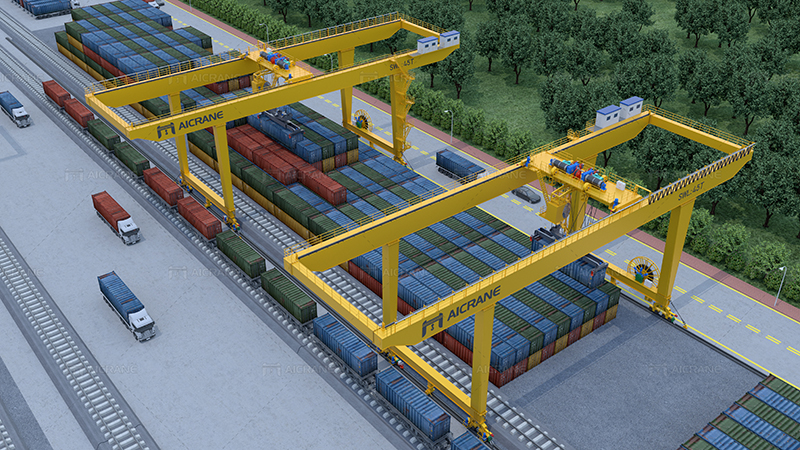
Control System and Automation
The control system of an RMG crane plays a significant role in its operational efficiency. Modern cranes often come equipped with advanced control systems that allow for precise movements and automated functions.
Impact on Efficiency: Automation can significantly enhance efficiency by reducing the need for manual intervention and minimizing human error. Features like automated stacking, remote control operation, and anti-sway technology allow for faster and more accurate load handling. A sophisticated control system can also improve safety, further contributing to operational efficiency.
Optimization Tip: Investing in a crane with an advanced control system and automation features can be particularly beneficial in large-scale operations where speed, precision, and safety are paramount. Businesses should consider the level of automation that best suits their operational needs and budget.
Durability and Material Specifications
The materials used in constructing the RMG crane, as well as its overall durability, are critical for ensuring long-term efficiency.
Impact on Efficiency: A crane built with high-quality, durable materials will require less maintenance and have a longer lifespan, leading to fewer disruptions in operations. Additionally, durable cranes are better suited to withstand harsh environmental conditions, which can be a common challenge in outdoor or industrial settings.
Optimization Tip: When selecting an RMG crane, it’s important to consider the environmental conditions it will operate in and choose materials that are resistant to corrosion, wear, and other forms of degradation. Regular maintenance and using the appropriate materials for repairs can also help in maintaining the crane’s efficiency over time.
Energy Efficiency
Energy consumption is an often-overlooked specification that can have a significant impact on the operating costs and overall efficiency of an RMG crane.
Impact on Efficiency: Energy-efficient cranes reduce operational costs by consuming less power during operation. This is particularly important in large facilities where cranes may be in continuous use. Additionally, energy-efficient cranes often generate less heat and noise, contributing to a better working environment.
Optimization Tip: Look for cranes that feature energy-saving technologies, such as regenerative drives, which can convert kinetic energy into electrical energy during braking. These systems not only save energy but also reduce wear and tear on the crane’s components.
Safety Features
Safety features are an integral part of the crane’s specifications and have a direct impact on efficiency.
Impact on Efficiency: Cranes equipped with advanced safety features such as overload protection, anti-collision systems, and emergency stop functions can prevent accidents and damage to goods. Fewer accidents mean less downtime and fewer disruptions in operations, leading to a more efficient workflow.
Optimization Tip: Prioritize cranes that offer comprehensive safety features. While these may add to the initial cost, the long-term benefits in terms of reduced downtime and enhanced safety make them a worthwhile investment.
Customization and Flexibility
Finally, the ability to customize the RMG crane to meet specific operational needs can significantly enhance its efficiency.
Impact on Efficiency: A crane that is tailored to the unique requirements of a facility will perform more efficiently than a standard model. Customizable features such as interchangeable spreaders, variable lifting speeds, and specialized controls can improve the crane’s adaptability and effectiveness in different scenarios.
Optimization Tip: Work with manufacturers like Aicrane who offer customization options. By specifying exactly what your operation needs, you can ensure that the crane will function optimally in your specific working environment.
The specifications of a rail mounted gantry crane are more than just technical details; they are critical factors that directly influence the crane’s working efficiency. By carefully selecting a crane with the appropriate lifting capacity, span length, lifting height, speed, control system, durability, energy efficiency, safety features, and customization options, businesses can optimize their operations, reduce costs, and improve productivity. Understanding how each specification impacts efficiency allows for informed decision-making and ensures that the chosen RMG crane will meet the demands of the operation both now and in the future.